PENGELASAN DIBAWAH PERMUKAAN AIR LAUT (UNDERWATER WELDING)
Teknologi pengelasan (welding) sering sekali digunakan untuk memperbaiki kerusakan yang terjadi pada badan kapal, bangunan lepas pantai serta konstruksi lainnya yang terendam air. Pada pelaksanaannya, pengelasan di permukaan air masih merupakan prioritas utama sedangkan pengelasan di bawah air adalah alternatif lain yang dipilih bilamana tidak memungkinkan untuk dikerjakan di permukaan air.
Ada beberapa keuntungan yang didapat dari teknik pengelasan ini, diantaranya adalah biaya yang relatif lebih murah dan persiapan yang dibutuhkan jauh lebih singkat dibanding dengan teknik yang lain, namun ada hal-hal lain yang mesti dipertimbangkan sebelum mengaplikasikannya. Selama masa operasinya, struktur lepas pantai akan membutuhkan beberapa intervensi bawah air untuk perawatan, perbaikan atau perubahan, seperti:
- Penguatan untuk resertifikasi struktur yang telah habis desain life-nya.
- Perbaikan karena kesalahan desain.
- Perbaikan karena kerusakan yang disebabkan oleh:a. Kesalahan pada saat instalasi,b. Insiden, misalkan tertabrak kapal, badai,c. kejatuhan benda dari atas dek, dan sebagainya,d. keretakan pada sambungan karena keadaan lingkungan (ombak, angin).
- Penambahan struktur karena adanya perubahan operasi (pemasangan riser, clamp, caisson, dan sebagainya).
- Pemasangan anode
- Grinding out cracks
- Clamps
- Grout filling
- Pengelasan hyperbaric
- Pengelasan bawah air
Terdapat beberapa pihak belum tertarik untuk menerapkan teknik pengelasan di bawah permukaan air. Hal ini terbukti bahwa hanya ada 50 kegiatan pengelasan bawah air untuk perbaikan struktur lepas pantai yang dipublikasikan selama 40 tahun terakhir, itu juga dengan sedikit informasi yang bersifat teknik. Pihak industri masih tertarik untuk memakai pengelasan hyperbaric atau pemasangan clamp meskipun butuh persiapan yang lebih rumit dan biaya yang lebih mahal.
- Kendala pada Underwater WeldingKeengganan pihak industri untuk memakai teknik pengelasan bawah air ini bisa dimengerti mengingat hal-hal berikut :a. Class, baik DNV atau LR belum menerima teknik ini untuk perbaikan yang sifatnya permanen. Terdapat weld defects yang hampir selalu menyertai (porosity, lack of fusion, cracking) yang memberatkan teknik pengelasan ini untuk tujuan-tujuan perbaikan permanen. Pada perbaikan elemen yang dapat dikatakan kurang penting, class sudah bisa menerimanya sebagai permanen bersyarat yaitu bisa dianggap sebagai permanen asal dalam inspeksi mendatang tidak ditemukan penurunan yang signifikan dari kualitas pengelasan.b. Mengacu pada AWS D3.6:1999 yaitu Specification for underwater welding, hasil terbaik yang bisa diperoleh dari teknik ini adalah baru Class B. Hasil seperti ini hanya bisa diterima kalau tujuan pengelasan hanya untuk aplikasi yang kurang penting/kritis dimana ductility yang lebih rendah, porosity yang lebih banyak, discontinuities yang relatif lebih banyak masih bisa diterima. Kalaupun pengelasan ini dipakai biasanya hanya diaplikasikan untuk tujuan-tujuan yang sifatnya ‘fit for purpose’ saja.c. Tingginya resiko hydrogen cracking di area HAZ terutama untuk material yang mempunyai kadar karbon equivalent lebih tinggi dari 0.4%. Terutama di Laut Utara, struktur lepas pantainya biasa menggunakan material ini.d. Berdasarkan pengalaman yang ada di industri, teknik pengelasan ini hanya dilakukan sampai kedalam yang tidak lebih dari 30 meter.e. Kinerja proses shieldedmetal arc (SMA) dari elektroda ferritic memburuk dengan bertambahnya kedalam. Produsen elektroda komersial juga membatasai penggunaannya sampai kedalaman 100 meter saja.f. Sifat hasil pengelasan juga memburuk dengan bertambahnya kedalaman, teruatama ductility dan toughness (charpy impact).g. Karena kontak langsung dengan air, maka air di sekitar area pengelasan menjadi mendidih dan terionisasi menjadi gas oksigen dan hidrogen. Sebagian gas ini melebur ke area HAZ tapi sebagian besar lainnya akan mengalir ke udara. Bila aliran ini tertahan, maka akan terjadi resiko ledakan yang biasanya membahayakan penyelam.
- Pemecahan Masalah dari Underwater WeldingMeskipun ada beberapa kendala yang membuat pihak industri yang enggan untuk memakai teknik pengelasan ini, sebenarnya terdapat beberapa usaha perbaikan yang telah dilakukan, baik dalam teknik pengelasan maupun mutu elektrodanya, yaitua. Hydrogen cracking dan hardness di area HAZ bisa diminimalisasi atau dihindari dengan penerapan teknik multiple temper bead (MTB). Konsep dari teknik ini adalah dengan mengontrol rasio panas (heat input) diantara lapisan-lapisan bead pengelasan. Pengontrolan panas ini, ukuran bead pada lapisan pengelasan pertama harus disesuaikan sehingga penetrasi minimum ke material bisa didapat. Begitu juga untuk lapisan yang kedua dan seterusnya.b. Terdapat tiga parameter yang mempengaruhi kualitas pengelasan dalam penerapan MTB ini, yaitu jarak antara temper bead, rentang waktu pengelasan, dan heat input.c. Teknik buttering juga bisa digunakan terutama untuk material dengan CE lebih dari 0.4%. Elektroda butter yang digunakan bisa elektroda yang punya oxidizing agent atau elektroda thermit.d. Pemakain elektroda dengan oxidizing agent. Agent ini akan menyerap kembali gas hidrogen atau oksigen yang terserap di HAZ.e. Pemakaian thermit elektroda juga bisa digunakan. Elektroda jenis ini akan memproduksi panas yang tinggi dan pemberian material las (weld metal) yang sedikit sehingga mengurangi kecepatan pendinginan dari hasil pengelasan oleh suhu di sekitarnya sehingga terjadi semacam proses post welding heat treatment.f. Elektroda berbasis nikel bisa menahan hidrogen untuk tidak berdifusi ke area HAZ. Sayangnya hardness di area HAZ masih tinggi dan kualitas pengelasan hanya baik untuk kedalaman sampai 10 meter.
- Metode Pengelasan pada Pengelasan Bawah AirMetode perbaikan akan dibutuhkan seperti pengelasan bawah air (underwater welding). Dua kategori utama pada teknik pengelasan di dalam air adalah pengelasan basah (Wet Underwater welding) dan pengelasan kering (Dry Underwater Welding).
- Pengelasan Basah (Wet Underwater Welding)Dimana proses pengelasan ini berlangsung dalam keadaan basah dalam arti bahwa elektrode maupun benda berhubungan langsung dengan air. Applikasi pengelasan sampai kedalaman 150 m. Metode pengelasan memberikan hasil yang kurang memuaskan, disamping memerlukan welder yang memiliki keahlian menyelam yang tangguh dan memerlukan pakaian khusus untuk selam, gelembung gas yang terjadi selama proses pengelasan akan sangat mengganggu pengamatan welder tersebut. Adapun proses pengelasan yang dipakai SMAW, FCAW dan MIG.Shielded metal arc welding (SMAW) adalah proses pengelasan dengan mencairkan material dasar yang menggunakan panas dari listrik antara penutup metal (elektroda). SMAW merupakan pekerjaan manual dengan peralatan meliputi power source, kabel elektroda, kabel kerja (work cable), electrode holder, work clamp, dan elektroda. Elektroda dan system kerja adalah bagian dari rangkaian listrik.Flux cored arc welding (FCAW) merupakan las busur listrik fluk inti tengah / pelindung inti tengah. FCAW merupakan kombinasi antara proses SMAW, GMAW dan SAW. Sumber energi pengelasan yaitu dengan menggunakan arus listrik AC atau DC dari pembangkit listrik atau melalui trafo dan atau rectifier. FCAW adalah salah satu jenis las listrik yang memasok filler elektroda secara mekanis terus ke dalam busur listrik yang terbentuk di antara ujung filler elektroda dan metal induk.Metal inert gas (MIG) adalah juga las busur listrik dimana panas yang ditimbulkan oleh busur listrik antara ujung elektroda dan bahan dasar, karena adanya arus listrik. Pengelasan MIG secara luas digunakan setiap kali dibutuhkan peleburan/penyatuan logam dengan kecepatan tinggi dan sedang.Gambar (a) cara kerja shielded metal arc welding, (b) cara kerja flux cored arc welding (c) carakerja metal inert gas
- Pengelasan Kering (Dry Underwater Welding)Metode pengelasan ini tidak berbeda dengan pengelasan pada udara terbuka. Hal ini dapat dilakukan dengan bantuan suatu peralatan yang bertekanan tinggi yang biasa disebut dengan Dry Hyperbaric Weld Chamber, dimana alat ini secara otomatis didesain kedap air seperti layak desain kapal selam. Applikasi pengelasan sampai kedalaman 150 m kebawah. Seorang welder /diver sebelum menjalankan tugas ini tidak boleh langsung terjun pada kedalaman yang dituju, tetapi harus menyesuaikan terlebih dahulu step by step tekanan yang terjadi pada kedalaman tertentu sampai dapat menyesuaikan tekanan yang terjadi pada kedalaman yang dituju, otomatis untuk pengelasan 1 joint bisa memakan waktu yang cukup lama.
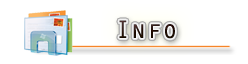
Link Download :
Password : | Status : Tested (Windows 8)
Facebook: Indar luh sepdyanuri
Twitter: Indar Luh Sepdyanuri
G+: +IndarLuhSepdyanuri
BBM : 7962E731
Whatsapp : 087738325051
Line : Indar Luh Sepdyanuri